What does a typical food & beverage supply chain look like?
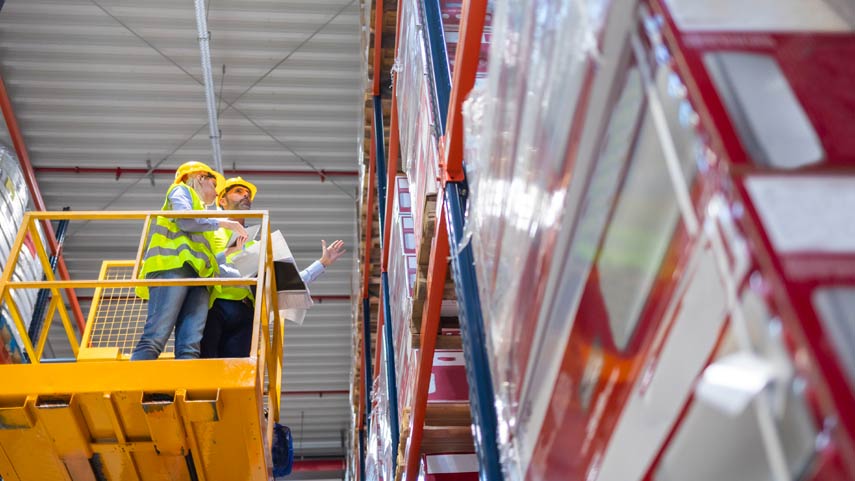
Foundational to safe and reliable food transportation is an understanding of the food and beverage supply chain. Simply put, a supply chain is defined by all the steps that must occur to conceive, create, deliver, and distribute products.
The food and beverage supply chain refers to the process by which raw materials and ingredients are sourced, processed, and distributed to customers. It involves many stakeholders, including farmers, processors, distributors, retailers, and consumers.
The flow of food in the supply chain typically moves in the following order:
- raw goods and materials are produced through farmers or growers
- materials are transported to mills or processing facilities to create finished products
- products are sent to warehouses and distribution centers
- products are shipped to retailers like restaurants and supermarkets
- products are sold to customers and end consumers purchasing the foods and beverages
The supply chain processes within the food and beverage industry are complex and require seamless coordination from start to finish. Here, we’ll examine the key pieces of supply chain management (SCM) and its role in the food and beverage industry.
What are the core elements of a food and beverage supply chain?
All the building blocks of a food and beverage supply chain work together to manage the flow of materials, products, and information. By optimizing the performance of each of the following elements, food and beverage companies can improve the overall efficiency and effectiveness of their supply chain.
Integration
Integration within a food and beverage supply chain refers to the alignment of processes and systems across different functional areas within the supply chain. This includes coordination between growers, manufacturers, distributors, retailers, and customers to ensure that products are produced, transported, and delivered in a timely and efficient manner—all while maintaining food safety and quality standards
Proper, proactive coordination among all parties across the supply chain will save an organization time, money, and mistakes in the long run. Integrating each step of the supply chain process also provides a clearer picture of how overall operations are running and any areas for improvement.
While Graham C. Stevens created the framework for the supply chain integration model in 1989, it’s still widely used for understanding the different levels of integration that organizations can strive to achieve. Stevens breaks down integration into four stages:
- Baseline: This is the starting point for organizations to understand their current supply chain operations. It involves identifying and analyzing key performance indicators (KPIs) and processes, as well as identifying areas for improvement.
- Functional Integration: Integrating specific functional areas within an organization, such as purchasing and logistics. The goal is to improve the efficiency and effectiveness of these functional areas by streamlining processes, reducing lead times, and minimizing inventory.
- Internal Integration: Aligning and coordinating the activities of different functional areas within an organization. It involves implementing a standard set of processes and systems to ensure that all departments work towards the same goals.
- External Integration: Integrating the activities of external partners, such as suppliers and customers. It involves implementing collaborative processes and systems to enable real-time communication and data sharing, as well as developing long-term partnerships to support mutual growth and success.
Operations
Tracking daily operations across the food and beverage supply chain ensures that all processes stay on track. There are several ways to track daily operations in a food and beverage supply chain, including:
- Automated systems: Automated systems such as enterprise resource planning (ERP) software and warehouse management systems (WMS) can track inventory levels, production schedules, and logistics in real time. These systems can also integrate with other systems, such as quality management systems (QMS) and traceability systems to provide a complete view of supply chain operations.
- Barcode scanning and RFID (Radio-Frequency Identification): Barcode scanning and RFID technology can track products as they move through the supply chain, from the farm to the consumer. This can provide real-time visibility into the location and status of products, as well as a record of all product movements.
- Dashboards and reporting: Dashboards and reporting tools can monitor KPIs such as inventory turnover, on-time delivery, and lead times. These tools can provide an overview of supply chain operations, highlighting any areas that require attention and enabling managers to make informed decisions.
- Mobile technology: Mobile devices and apps can track operations in the field. For example, logistics personnel could use mobile devices to track the delivery of goods in real time. Field workers could also use mobile devices to collect data on crop yields and quality.
- Collaboration with suppliers and partners: Collaborating with suppliers and partners can provide real-time visibility into the activities of external organizations and can help to identify potential issues and opportunities.
Purchasing
Companies must determine which goods, tools, and materials to purchase for their needs. After all, if they run short on these resources, it may disrupt and delay the supply chain. Expertise from qualified employees and purchasing managers with knowledge of inventory management is crucial to a strong supply chain.
In the food and beverage supply chain, the goods, tools, and materials required can vary depending on the specific products and operations involved. However, some of the common purchases required include:
- Raw materials: Ingredients and raw products such as grains, fruits, vegetables, meat, and dairy products.
- Packaging materials: Materials such as cans, bottles, cartons, and trays.
- Processing equipment: Equipment used to process and manufacture food and beverage products, such as mixers, blenders, ovens, and packaging machines.
- Transport equipment: Vehicles and equipment used to transport food and beverage products, such as trucks, refrigerated containers, and pallets.
- Logistics software: Software used to manage logistics operations, such as a WMS, transportation management systems (TMS), and ERP software.
- Quality control equipment: Equipment used to monitor and maintain food safety and quality standards, such as temperature and humidity sensors, pH meters, and microscopes.
- Traceability software: Software that helps to track and trace products through the supply chain.
Distribution
The food distribution supply chain involves activities such as receiving and storing inventory, fulfilling orders, and ultimately delivering products to customers—whether on shelves in-store or by shipping directly to their homes. This involves careful planning and logistics to ensure proper handling and efficient delivery to consumers.
Distribution in the food and beverage supply chain is critical as it ensures companies can deliver products in a fresh and timely manner, which is essential for perishable products. It also plays a vital role in maintaining food safety, as products must be stored and transported in a way that meets safety and quality standards. Effective distribution also enables food and beverage companies to meet customer needs by providing products that are in demand.
A typical food distribution supply chain might include:
- Transportation: The movement of products from the manufacturer or producer to distribution centers or warehouses, then to retailers or other end customers. This is typically done using trucks, trains, or ships and may involve multiple modes of transportation.
- Warehousing and storage: The storage of products in warehouses or distribution centers, which may include the use of refrigerated storage for perishable products.
- Order fulfillment: Receiving and processing orders from retailers or other end customers, and then preparing and shipping the products to their destination.
- Delivery: The final step of getting products to the end customer, whether to a retail store, a restaurant, or directly to the consumer.
- Reverse logistics: The movement of products back up the supply chain, such as returns, recalls, and disposals.
Food and beverage vs. other supply chains
In comparison to other supply chains, the food and beverage industry is distinct due to the perishable nature of food and drinks. The unique characteristics of food and beverage products require additional steps to ensure the safety and quality of products and manage the logistics accordingly.
Continuous flow supply chain
As a whole, the food and beverage supply chain relies more on a continuous flow model, producing goods on a consistent basis with little fluctuation in demand. However, there are some exceptions to this—such as seasonal produce and other food products.
Food products are subject to strict standards to ensure they are safe for human consumption. Preserving products is a priority for perishable items, as is the ability to reliably trace them through the supply chain in the case of a recall. Carriers may need to use refrigerated trucks—or “reefers”—to transport cold goods.
Thus, shipping food requires its own set of government regulations and safety practices. This means that companies in the food and beverage industry must take additional steps to ensure food safety, such as implementing Hazard Analysis and Critical Control Points (HACCP) systems, conducting regular testing and inspections, and adhering to strict sanitation requirements.
Other supply chain models
While the food supply chain model is based around food safety, other supply chains operate with different driving forces. For instance, the top priority of “fast fashion” companies within the clothing industry is to evolve and distribute clothes quickly through a fast chain model. It involves trends with short life cycles that must land on the market as soon as possible before they become irrelevant.
You could also consider goods that flow within a flexible supply chain model, with peak periods of high demand before significant drops in demand. This requires adaptability to customer needs and manufacturing schedules relating to factors like seasonality and holidays.
Examples of efficient food supply chains
Although companies dealing with food and beverage may have different supply chain strategies and business models, the successful ones share the common practices to drive efficiency. They use technology and automation to optimize operations, have a well-defined and integrated logistics network, and make use of advanced inventory management techniques.
Based on The Gartner Supply Chain Top 25 Companies for 2022, some corporations that exhibit efficient food supply chains include:
PepsiCo
PepsiCo employs a complex supply chain management system to guarantee its carbonated beverages are always available to customers. It receives raw materials from quality suppliers, leading to quality product output. The company directly delivers to stores to minimize how long their products spend within the supply chain.
Walmart
Walmart has a large network of retail stores and distribution centers, as well as a sophisticated inventory management system. In active partnership with food and beverage suppliers, Walmart also has one of the largest private trucking fleets in the United States. Its large logistics and transportation network allows its products to move to stores quickly.
McDonald’s
McDonald’s is known for its efficient supply chain in the food industry. It has a large network of suppliers and manufacturers and uses advanced logistics management systems to ensure that restaurants have the food and beverage products they need. McDonald’s also has a reliable, well-defined system for controlling and monitoring food safety.
How freight modes impact the food and beverage supply chain
The type of freight shipping mode can have a significant impact on the food and beverage supply chain in terms of transportation speed and cost, as well as food safety and quality.
Full Truckload (FTL)
Shipping with full truckload means the entire truck would be utilized for one shipper’s products or goods.
FTL Shipping Pros
- Cost-effective for larger shipments: FTL shipping can be cost-effective for companies that need to transport large quantities of goods, as the cost of the truck is spread across the entire shipment.
- Faster delivery: Since the truck is dedicated to a single customer, FTL shipping can be faster than other shipping methods, as there are no other pickups or deliveries along the route.
- Reduced handling: FTL shipping can reduce the amount of handling that products need to go through, which can help to reduce the risk of damage or spoilage.
- Greater control: FTL shipping enables companies to have greater control over the transportation of their products, as they can specify the route, delivery schedule, and other details of the shipment.
FTL Shipping Cons
- Limited flexibility: FTL shipping may not be suitable for companies that need to ship smaller quantities of goods or have irregular shipping schedules.
- Higher costs for smaller shipments: For companies that do not have enough products to fill a full truckload, the cost per unit may be higher than with less than truckload (LTL) shipping.
- Rigid delivery schedules: Since the truck is dedicated to a single customer, FTL shipping may not be suitable for companies that need to change delivery schedules or routes at short notice.
Less than truckload (LTL)
For lighter loads, less than truckload shipments take up less than an entire truck. Carriers combine multiple shipments, and routes are often organized based on regional hubs or terminals for transloading.
LTL Shipping Pros
- Lower upfront cost: LTL shipping can be cost-effective for companies that need to transport smaller quantities of goods, as the cost of the truck is spread across multiple customers.
- More frequent deliveries: LTL shipping can provide more frequent deliveries than FTL, as the truck can make multiple pickups and deliveries along the route.
- Pickup and delivery services: Many LTL carriers offer pickup and delivery services, which can be convenient for companies that do not have the resources to transport their goods to the carrier’s terminal.
LTL Shipping Cons
- Hidden fees: Shippers can have difficulty predicting LTL pricing, as there can be several hidden fees. These can include accessorial fees, late fees, and fees related to damage claims.
- Less control: LTL shipping can provide less control over product transportation, as the route, delivery schedule, and other details are determined by the carrier.
- Greater handling: LTL shipping increases the amount of handling that products need to go through, as goods are consolidated with other customers’ goods, increasing the risk of damage or spoilage.
- Longer delivery times: Since the truck makes multiple pickups and deliveries along the route, LTL shipping often results in late deliveries.
Partial truckload (PTL)
Partial truckloads consolidate freight that won’t require a full truckload while keeping goods on one truck. Shipments are matched for compatibility in real time, so goods aren’t waiting around for truckloads headed in the same direction.
PTL Shipping Pros
- Cost-effective compared to FTL: PTL shipping can be a cost-effective option for companies that need to move shipments that are larger than LTL but still less than a full truckload, as the cost of the truck is shared among multiple customers.
- Less chance of damage and faster transit times: PTL shipments are usually a direct route to the destination, which means the same truck that picks up the shipment also delivers it. This minimizes the chance for cargo damage, as well as increases the chances of faster transit times.
- No freight class requirements: Unlike LTL, PTL prices are quoted based on the total amount of trailer space required.
PTL Shipping Cons
- Limited control: PTL shipping can provide less control over the transportation of products as the route, delivery schedule, and other details may be determined by the carrier.
- Longer transit times: PTL shipping means space on a truck is shared with other customers’ goods, meaning the truck has to make additional stops before it will reach your intended dropoff location.
- Stringent specifications: PTL is only available to companies shipping 5,000 to 40,000 pounds of goods, or somewhere between 5-14 pallets. This specific prerequisite means PTL is not a common way of shipping.
Shared truckload (STL)
To maximize speed and avoid hidden costs, Flock Freight’s unique shared truckload shipping mode pools multiple shipments into one truckload and travels directly to its destination without transloading. Optimized routes with fewer stops lead to 30% more on-time deliveries than LTL. Reduced product handling not only ensures food safety but also incurs 5.7x less damage than traditional LTL—which means fewer dings to profits for food and beverage producers.
Let’s break down some of the key advantages of STL shipping with Flock Freight:
STL Shipping Pros
- Cost-effective for freight of all sizes: STL shipping is cost-effective for companies transporting freight of all sizes. With STL, shippers will only pay for the space they need, and they can ship goods as soon as they’re ready instead of waiting to fill an entire truck.
- Minimal risk of damage: STL shipments move terminal-free and provide a direct route to the destination using a single truck and driver—resulting in a 99.8% chance for goods to arrive damage free.
- More on-time delivery: STL shipping is faster than LTL shipping as it uses a multi-stop full truckload along the most efficient routes to reduce transit times. Flock Freight’s patented technology uses predictive pooling algorithms to match locations, schedules, and compatible shipments. STL shipping also gives shippers complete control of pickup and delivery dates.
- No hidden costs: There are no last-minute charges, LTL corrections, or other hidden costs such as accessorial fees or linear foot caps with STL shipping.
- Real-time tracking: Flock’s platform provides real-time tracking of shipments, so companies can monitor the progress of their goods throughout the journey.
Challenges in the food and beverage supply chain
Food and beverage supply chain challenges are plentiful and specific to the industry. Some issues that can arise include:
- agricultural complications like pests, bad weather, and market prices for crops
- food contamination risks
- managing special safety regulations and inspections to prevent foodborne illnesses
- limited tracking systems that impair traceability of food products
- and more
Explore more about the food and beverage supply chain in the next chapter of this guide: 7 Challenges of the Food & Beverage Supply Chain
Not shipping food and beverage? Learn more about shared truckload for your industry.